Sand is in high demand
With more than 100 years of experience, Zandhandel‘s Faasse dredging activities have increased significantly in recent years. This family-owned company specialises in maintenance dredging of shallow waterways on both the Dutch and Belgian plateaus. Zandhandel Faasse annually (2019) extracts three million tonnes of sand used for, for example, drainage, the concrete industry, infrastructure, sports fields, and beach spraying.
Strong reputation and support
Zandhandel Faasse was approached by FLSmidth in 2016 together with Delta pompen B.V. as a third party. They had not realised FLSmidth could provide pumps for dredging on ships. Following a good consultation and after looking at the experience of the team and the capabilities of the FLSmidth pumps, Zandhandel Faasse decided to take a chance on a pump for his new ship, the Scald.
The millMAX™ pump: a great match for the ship
The Scald is a durable trailing suction hopper dredger (TSHD) with an unlimited sailing area, shallow draft, and special manoeuvring properties due to four rudder propellers and a liftable wheelhouse. Benefits of the millMAX™ pump
- High slurry efficiencies
- Reduced power costs
- Reduced maintenance costs
- Increased availability
- Increased wear lifetime
Keeping suction and discharge pressure constant
The advantages of the millMAX pump design include lower power requirements; long, even wear life; and less pump downtime – all of which result in a lower cost-per-ton pumped, along with better cyclone separation.
The most important aspect of dredging is the suction, which determines how much sand you can get, and the millMAX pump has definitely lived up to the expectations. The design includes the wear ring that means an adjustable assembly, permitting the closing of the suction-side impeller clearance during operation. The pump has operated without any need for repair or spare parts since its installation more than 3 years ago.
The suction wear ring helps to keep the vacuum in the suction head over the complete lifetime of the pump. Eliminating wear on the suction liner and enlargement of the impeller eye means that there is no loss of vacuum or efficiency, and fuel consumption remains low and constant. There is also no need to speed up the pump to compensate for recirculation losses between discharge pressure and the suction wear plate.
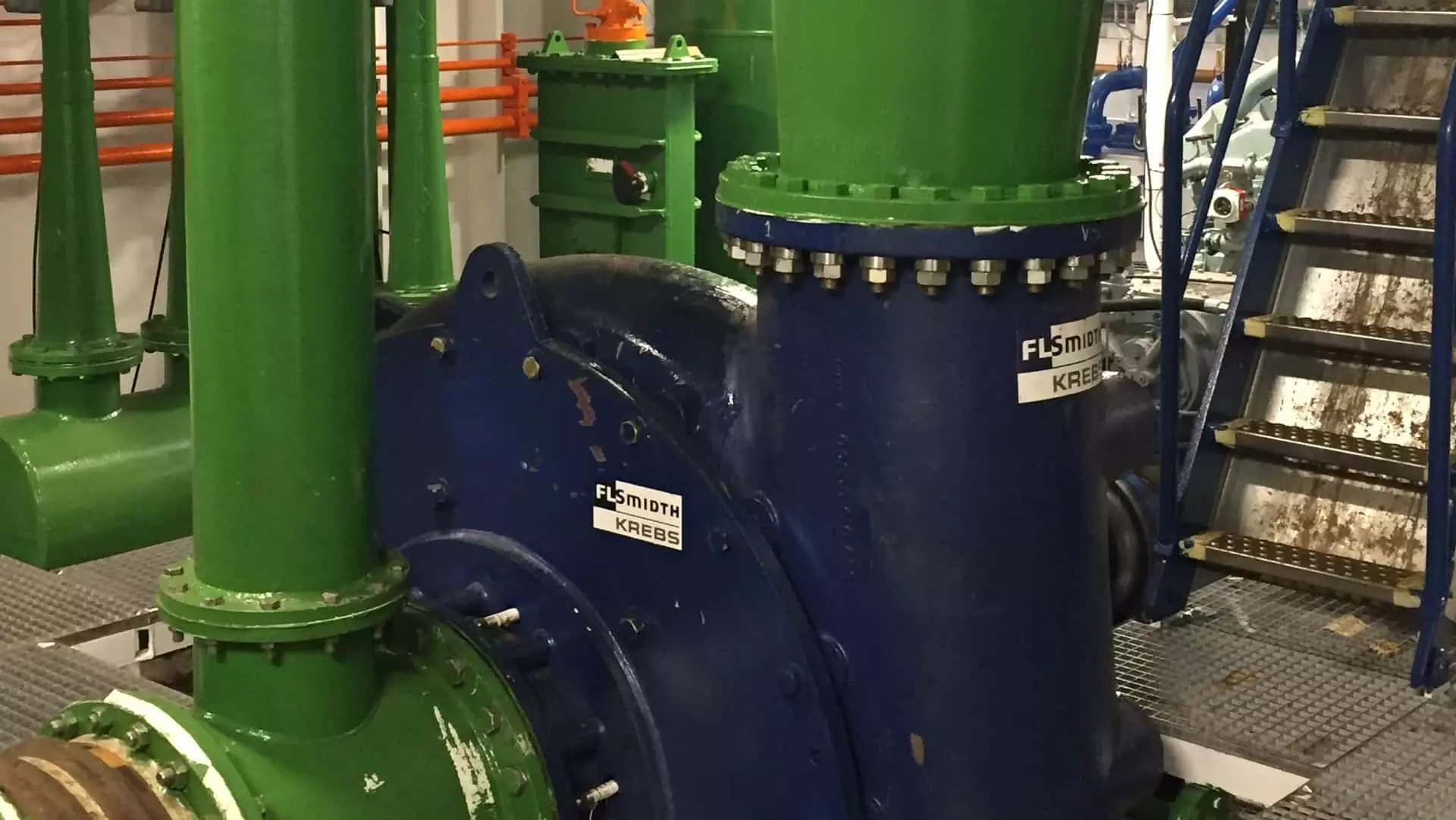
In addition, the vacuum sensors were a really important part of the design for Faasse Zandhandel. The vacuum sensors keep the suction pressure and the discharge pressure constant, so the Scald doesn’t lose pressure, making the dredging easier and more efficient. It’s also safer because the reliability means that operators avoid having to do dangerous repairs.
The main advantage in production is the unmatched vacuum, which enables to get more sand in a shorter dredge time and without the risk of sanding the suction pipe. It saves time, fuel and maintenance downtime with this pump.
Minimal downtime for maintenance
According to Zandhandel Faasse they have noticed less wear as a result of eliminating the grinding of solids between the front side impeller and the suction liner. And there is no need to adjust the bearing frame towards the suction liner to compensate for loss of hi-chrome material in the casing and the impeller. Overall, less maintenance shutdown is required.
The Scald can achieve higher sand content over the complete lifespan of the pump, with higher solids concentration and almost no sanding of the suction pipe or dredge head. In addition, the grease-lubricated heavy-duty power frame, which is designed to eliminate the possibility of over-greasing, means that there is no need for an oil cooler system on the bearing frame and this saves money and maintenance time.
Ship name: The SCALD
Main dredge pump: MillMAX 24x20 (600 mm pump)
Booster pump: MillMAX 24x20 (600 mm pump)
Medium: Sea sand and organic sludge
Solids density: 2,7 kg/l
Liquid density: 1 kg/l
Slurry density: 1,4 kg/l
Solids concentration: 50 %Cw <0,1 mm
Pump proves itself onboard
Capable of pumping 4000m3 of water, and with an 8-bar discharge pressure, the Scald can pump over a long landline and reach an inland sand plant to unload. The millMAX has proved itself in dredging: “The millMAX dredge pump has been in operation on the Scald for 3 years now and we are very satisfied. We‘ve had continued commitment and support from FLSmidth during the operation. And no spare parts have been needed so far at all!” says Zandhandel Faasse.
In particular, Faasse Zandhandel is enjoying the following excellent results from the millMAX pump installation:
- Better contracts because of the 8-bar discharge pressure capability
- Higher efficiency due to the narrow wearing clearance
- Improved vacuum, which increases the sand concentration
- Reduced clogging of the dredge arm
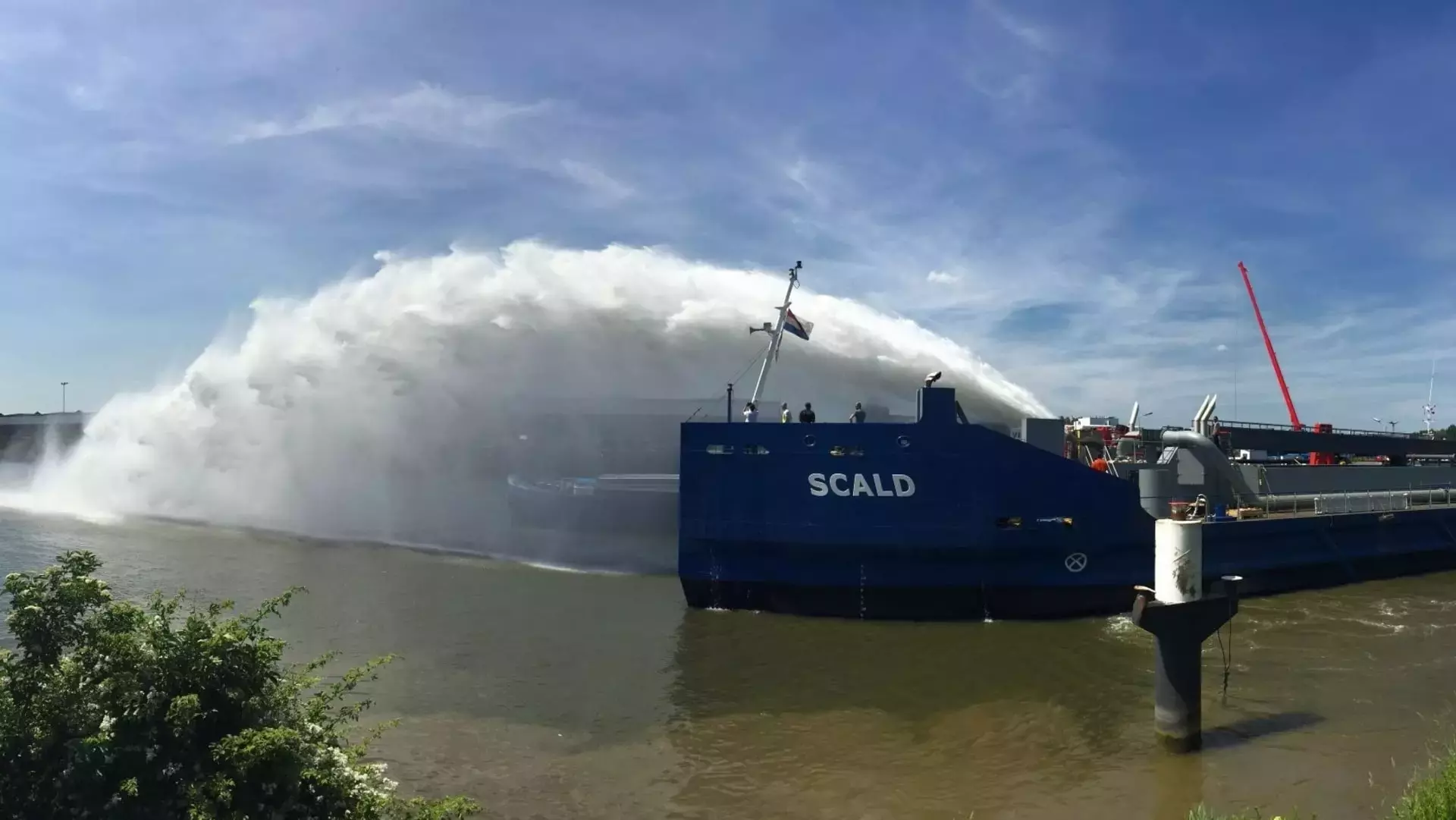
The future is sustainable
Following the success of the dredging pump on the Scald, the management at Zandhandel Faasse knew that FLSmidth together with Delta pompen B.V. as third party could handle quality and sustainability and could deliver advanced, reliable pumps, so the company commissioned another millMAX pump for a different ship, the Schenge.
The Schenge was completed in June 2020 and is being deployed for sand extraction in the North Sea; it has a hopper capacity of approximately 2600m3, divided over two holds, so it can carry two types of product. “For our new TSHD, completed in the first half of 2020, we decided on an even bigger FLSmidth millMAX 28x26 dredge pump,” says Zandhandel Faasse. “We continue to invest in sustainability and innovation to keep our fleet up-to-date and the millMAX pump on the Schenge is 100% electrically driven, helping to reduce diesel use and minimise emissions.”
With the new TSHD Schenge providing more contact sand the Scald is shifting into the maintenance dredging. This application, where the water is shallow and the sand is extremely abrasive, suits the MillMAX pump perfect since the wear impact on this pump is so low no other pump can compete.
-
KREBS® gMAX® Cyclone
-
gravelMAX™ pump
-
KREBS® vMAX™ Sump Pump